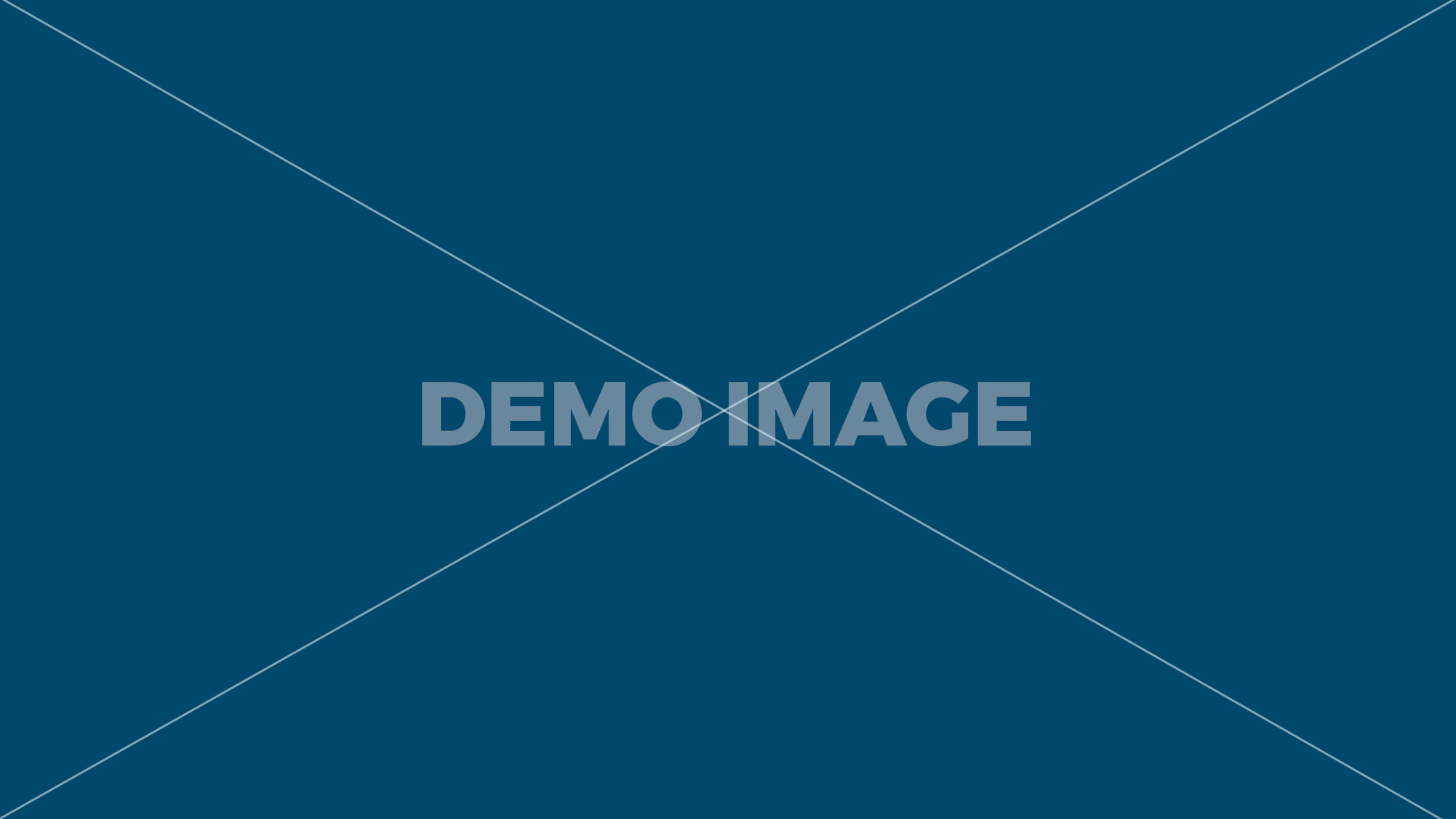
Figure 5 Ashby plot presenting the tensile strength parallel to the grain vs. the density for various wood species and thermoplastic productsÂ. Fillers can decrease density, strength … Polycarbonate is the preferred material when manufacturers want to use a hardy, transparent plastic, that they can easily incorporate colors and patterns with. Effects of Bone Particle on the Properties and Microstructure of Polypropylene/Bone Ash Particulate Composites. [ Links ], GWON, J. G. et al. [ Links ], JOSEPH, P. V. et al. In: INTERNATIONAL CONFERENCE ON WOOD & BIOFIBER PLASTIC COMPOSITES AND CELLULOSE NANOCOMPOSITES SYMPOSIUM, 10., Madison, 2010. [ Links ], BOWYER, J. et al. Philadelphia, 2013. 2009. The Influences of Fiber Feature and Polymer Melt Index on Mechanical Properties of Sugarcane Fiber/Polymer Composites. (2009) and Omar, Akil and Ahmad (2011), for example, had presented the composites densities, probably the specific compressive strength means (both parallel and perpendicular to grain) would be much lower, since these papers show composites' compressive values ranging from 3MPa to 40 MPa, while the plotted values range from 75MPa to 195MPa. [ Links ], NAUMANN, A.; STEPHAN, I.; NOLL, M. Material Resistance of Weathered Wood-Plastic Composites Against Fungal Decay. PP-carbonized cow bone powder and PP-uncarbonized cow bone powder exhibited the highest specific strength, followed by nylon composites. very few data were found on the compressive and shear strength of plastic lumber and thermoplastic composites. Wood strength, including the relationship between grain direction and strength, specific gravity as an indication of wood strength, and additional ways to measure wood strength. [ Links ], WEI, L. et al. Nonetheless, all experimental plastic-based product data plotted in Figure 11 are for a pure nylon product, nylon-silica fume composites, PP-carbonized cow bone powder, or PP-uncarbonized cow bone powder, as studied by Raja and Kumarave (2015) and Asuke et al. The same phenomenon was observed for commercialized thermoplastic products' flexural properties, as well as their tensile, compressive and shear properties. Only one thermoplastic-based material produced by a manufacturer has a tensile strength parallel to the grain similar to that of some wood species and, specifically, to the average of the coniferae species (about 67MPa); all other commercialized thermoplastic products have inferior tensile strengths parallel to the grain (Figure 5). Polymer Composites, v. 31, p. 185-194, 2010. MDF Dust/PP Composites Reinforced With Nanoclay: morphology, long-term physical properties and withdrawal strength of fasteners in dry and saturated conditions. Its manufacturing formulas enable it to use higher amounts of mineral filters, such as fly ash and gypsum, thus lowering production costs. Plastic bending is a nonlinear behavior particular to members made of ductile materials that frequently achieve much greater ultimate bending strength than indicated by a linear elastic bending analysis. Take that same part, now manufactured with aluminum, and the plastic version would be approx… Trex is a wood-plastic composite material designed for use in non-structural areas such as railing and decking. Note: Structural plastic lumber is not a direct replacement for wood… FRP vs Wood. No papers were found on the shear strength of thermoplastic products.Â. Effects of Wood Fiber Esterification on Properties, Weatherability and Biodurability of Wood Plastic Composites. The highest specific flexural modulus values for the experimental thermoplastic products were also found in PP-, HDPE- and PVC-based composites. Different data have also been collected from different books for some wood species. In both the plastic … Chloride) Strength (Tensile) Very good mechanical properties. Similar to the flexural modulus, the thermoplastic products that exhibited values of flexural strength comparable to those of wood have a much higher density. At least when compared to wood, this study found contrary results, although it embraces not only wood polymer composites and natural fiber-thermoplastic composites. [ Links ], SINGH, S. et al. Approximately 84% of the analysed dicotyledon wood species present densities below 900 kg/m3, while approximately 91% of the analysed thermoplastic products have densities above 900 kg/m3. But a judge for the 2012 Minnesota Cup — an entrepreneurial competition focusing on new, innovative businesses — says those two expectations are not true with Envirolastech. For all other properties, wood is still more efficient than thermoplastic products and composites, i.e., to support a given load, thermoplastic-based elements need to be much larger and heavier than those of wood (Figure 15). Plastic Lumber Tests Stronger Than Wood Lumber, Medical Device and Pharmaceutical Testing, Envirolastechâs âplastic lumberâ passes strength test, Polymer Film Changes Color to Signal Different Packaging Conditions, Medical Device Would Allow for Surgery in Zero Gravity, Space, Join Us For a Webinar on the Regulatory Aspects of Nitrosamines Testing, ASTM F1635-11 In vitro Degradation Testing of Hydrolytically Degradable Polymer Resins and Fabricated Forms for Surgical Implants, PSI’s Greatest Hits: Our 6 Most-Requested Polymer Tests. Wood-plastic composites (WPCs) are produced by thoroughly mixing ground wood particles and heated thermoplastic resin. Palavras-chaves: Compósito polimérico; Resistência; Propriedade especÃfica; Densidade; Seleção de material. 2014. Oxford: Elsevier, 2005. [ Links ], STARK, N. M.; ROWLANDS, R. E. Effects of Wood Fiber Characteristics on Mechanical Properties of Wood/Polypropylene Composites. Markets, Applications, and Processes for Wood Polymer Composites (WPC) in Europe. The strips are stapled where the strips cross. While only 13% of the 245 wood species show a density higher than 900 kg/m3, approximately 89% of the 171 thermoplastic products have densities higher than that. 2010. Good compressive properties, variable with the species of wood … Acesso em: 24 mar. The company has tested the plastic lumber and found that cold temperatures do not make it brittle, which is a common problem with plastics. Polyvinyl Chloride (PVC): Polyvinyl Chloride is perhaps most well known for its use in residential and … Composites Part A: Applied Science and Manufacturing, v. 39, n. 7, p. 1091-1100, jul. This work was supported by the Brazilian agency Coordenação de Aperfeiçoamento de Pessoal de NÃvel Superior (CAPES). It analyses the properties of wood from the coniferae and dicotyledon species and those of commercialized and experimental thermoplastic-based product formulations. 2009. Results in Physics, v. 2, p. 135-141, 2012. Five strength properties that are commonly measured for design purposes include bending, … [ Links ], ARAO, Y. et al. For the specific flexural modulus, the thermoplastic-based products showed lower property values than wood, even considering the best ratios presented by the former compared to the worst ratios of the latter. (2012). [ Links ], OMAR, M. F.; AKIL, H. M.; AHMAD, Z. European Journal of Wood and Wood Products, v. 69, n. 4, p. 553-556, 12 jan. 2011. Effects of Lubricant Content on Extrusion Processing and Mechanical Properties of Wood Flour-High-Density Polyethylene Composites. Schmidt spent eight years with the help of hired researchers to find the possibilities of combining various types of recycled products. Mechanical Properties and Failure Modes of Recycled Polypropylene/Microcrystalline Cellulose Composites. [ Links ], KOZÅOWSKI, R.; WÅADYKA-PRZYBYLAK, M. Review: flammability and fire resistance of composites reinforced by natural fibers. This is also a problem in the construction phase, as thermoplastic-based elements tend to be many times heavier than wood (in general, at least 2 times for elements under flexural loads (Figure 4) and 2.5 times for those under tensile loads parallel to the grain (Figure 6)), which make them difficult to transport and handle. Experimental plastic-based products have the highest compressive strengths parallel to the grain, some almost as high as 200 MPa. Nevertheless, in terms of durability and maintenance, studies have shown that plastic lumber provides a better performance than wood lumber (WINANDY; STARK; CLEMONS, 2004; GARCÃA et al., 2009; AZWA et al., 2013; NDIAYE; GUEYE; DIOP, 2013; WEI et al., 2013) and are also economically advantageous in the long term, as their maintenance can be performed less regularly and using simple products, such as soap and water. However, can they really substitute wood lumber products? Composites Part A: Applied Science and Manufacturing, v. 64, p. 90-98, 2014. For wood, density is expressed as pounds per cubic foot, kilograms per cubic meter, or grams per cubic centimeter - at a specified moisture content. In general, the commercialized thermoplastic products are at least 2.5 times less efficient than the other materials. [ Links ], AMERICAN SOCIETY FOR TESTING AND MATERIALS. Effect of Bark Fiber Content and Size on the Mechanical Properties of Bark/HDPE Composites. Popular Douglas Fir timber represents a flexural strength of up to 2800 psi. Polymer Testing, v. 27, n. 7, p. 801-806, out. 2001. [ Links ], MIGNEAULT, S. et al. Philadelphia, 2010a. Tensile strength … Figure 9 shows that the commercialized thermoplastic products have the lowest compressive strength parallel to the grain. Since many factors and procedures in the manufacturing process can change the density of the produced materials, it was considered that applying a simple rule-of-mixture to calculate the composites' densities would lead to unreal values. Use standard woodworking tools. An Overview of Mechanical Properties and Durability of Glass-Fibre Reinforced Recycled Mixed Plastic Waste Composites.  This is an Open Access article distributed under the terms of the Creative Commons Attribution License, which permits unrestricted use, distribution, and reproduction in any medium, provided the original work is properly cited. However, capacity can vary greatly depending on the pallet… When papers did not clearly presented the composites' density values, they were unappreciated in this study, even though the percentage and density of each material in the composites' formulation were described. It has been found in literature PP-wood flour and PP-wood fiber composites that reached static flexural strength over than 80MPa (NDIAYE; GUEYE; DIOP, 2013) and 90MPa (KARMARKAR et al., 2007), respectively, while (KIM et al., 2008) presents PP-cotton fiber composites that reached more than 200MPa; however as the composites' density values were not presented in the papers, the data were not considered in this study. Journal of Applied Polymer Science, v. 100, n. 5, p. 3641-3645, 5 jun. 2007. Figure 11 shows that the lowest values of the tensile strength perpendicular to the grain belongs to coniferae and dicotyledon wood species and to some commercialized thermoplastic products. In fact, just the opposite happens; the proprietary formula used in the plastic makes the plastic stronger in colder temperatures. This fact makes the design of structures and elements and the construction phase more complex; and. [ Links ], LU, J. Structural Properties of Recycled Plastic/Sawdust Lumber Decking Planks. Therefore, the analysis and graphs presented for each property covered in the Results section do not embrace all the considered wood species and thermoplastic-based product compositions. Mechanical properties: wood lumber versus plastic lumber and thermoplastic composites, Propriedades mecânicas: madeira versus madeira plástica e compósitos termoplásticos, 1Faculdades Multivix, São Mateus - ES - Brasil, 2Universidade Federal do EspÃrito Santo, Vitória - ES - Brasil. ASTM D4761: standard test method for mechanical properties of lumber and wood-base structural material. [ Links ], ENGLISH, B. W.; FALK, R. H. Factors That Affect the Application of Woodfiber-Plastic Composites. Industrial Fiberglass Vs… Figure 2 Specific modulus of elasticity of various wood species and thermoplastic productsNote: the mean of the 10% highest values, the mean of the 10% lowest values and the total mean of the materials' specific flexural strength were calculated using data from 50 coniferae wood species, 145 dicotyledon wood species, 83 experimental thermoplastic product compositions from 14 different papers and 17 commercialized thermoplastic product compositions from 12 manufacturers.Â. [ Links ], BOLIN, C. A.; SMITH, S. Life Cycle Assessment of ACQ-Treated Lumber With Comparison to Wood Plastic Composite Decking. Ashby plot presenting the modulus of elasticity vs. the density for various wood species and thermoplastic productsÂ, Specific modulus of elasticity of various wood species and thermoplastic productsNote: the mean of the 10% highest values, the mean of the 10% lowest values and the total mean of the materials' specific flexural strength were calculated using data from 50 coniferae wood species, 145 dicotyledon wood species, 83 experimental thermoplastic product compositions from 14 different papers and 17 commercialized thermoplastic product compositions from 12 manufacturers.Â, Ashby plot presenting the flexural strength vs. the density of various wood species and thermoplastic productsÂ, Specific flexural strength of various wood species and thermoplastic productsNote: the means of the materials' specific flexural strength were calculated using data from 50 coniferae wood species, 145 dicotyledon wood species, 141 experimental thermoplastic product compositions from 19 different papers and 20 commercialized thermoplastic product compositions from 18 manufacturers.Â, Ashby plot presenting the tensile strength parallel to the grain vs. the density for various wood species and thermoplastic productsÂ, Specific tensile strength parallel to the grain for various wood species and thermoplastic productsNote: the means of the materials' specific flexural strengths were calculated using data from 7 coniferae wood species, 43 dicotyledon wood species, 127 experimental thermoplastic product compositions from 17 different papers, and 12 commercialized thermoplastic product compositions from 9 manufacturers.Â, Ashby plot presenting the tensile strength perpendicular to the grain vs. the density for various wood species and thermoplastic productsÂ, Specific tensile strength perpendicular to the grain for various wood species and thermoplastic productsNota: the means of the materials' specific flexural strengths were calculated using data from 44 coniferae wood species, 130 dicotyledon wood species, 127 experimental thermoplastic product compositions from 17 different papers, and 11 commercialized thermoplastic product compositions from 9 manufacturers.Â, Ashby plot presenting the compressive strength parallel to the grain vs. the density for various wood species and thermoplastic productsÂ, Specific compressive strengths parallel to the grain of various wood species and thermoplastic productsNote: the means of the materials' specific flexural strength were calculated using data from 57 coniferae wood species, 188 dicotyledon wood species, 17 experimental thermoplastic product compositions from 2 papers and 24 commercialized thermoplastic product compositions from 19 manufacturers.Â, Ashby plot presenting the compressive strength perpendicular to the grain vs. the density for various wood species and thermoplastic productsÂ, Specific compressive strength perpendicular to the grain for various wood species and thermoplastic productsNote: the means of the materials' specific flexural strengths were calculated using data from 47 coniferae wood species, 75 dicotyledon wood species, 17 experimental thermoplastic product compositions from 2 papers, and 24 commercialized thermoplastic product compositions from 19 manufacturers.Â, Ashby plot presenting the shear strength vs. the density for various wood species and thermoplastic productsÂ, Specific shear strengths of various wood species and thermoplastic productsNote: the means of the materials' specific flexural strengths were calculated using data from 55 coniferae wood species, 179 dicotyledon wood species and 6 commercialized thermoplastic product compositions from 5 manufacturers. This study compares the modulus of elasticity and the flexural, compressive, tensile and shear strengths of such materials, as well as the materials' specific mechanical properties. Commercialized products have a higher specific strength than the coniferae and dicotyledon wood species, but the results of these three groups are not so different. Wood-Plastics Composites With Better Fire Retardancy and Durability Performance. Wood vs. Composite vs. Polymer. [ Links ], HEMMATI, F.; GARMABI, H. A Study on Fire Retardancy and Durability Performance of Bagasse Fiber/Polypropylene Composite for Outdoor Applications. 2015. [ Links ], LEI, Y. et al. (2014), as they exhibit a high deformation under small loads. This makes the design of structures and elements constructed with thermoplastic-based materials more complex, as they will occupy much more space or otherwise require many more components to satisfy a structural or semi-structural function, compared to wood. Mechanical data were collected from studies that used different standards to obtain values for the materials' density, modulus of elasticity and strength. In 1995, approximately 50 thousand tonnes of them were consumed in both regions. Studies on Physical and Mechanical Properties of Silica Fume-Filled Nylon 66 Polymer Composites for Mechanical Components. However, as the composites' density values were not presented in the papers, the data were not considered in this study. [ Links ], ADHIKARY, K. B. et al. Philadelphia, 2010b. [ Links ], AMERICAN SOCIETY FOR TESTING AND MATERIALS. Data on 146 polymeric and composite experimental formulations were from in scientific papers. [ Links ], FABIYI, J. S.; MCDONALD, A. G. Effect of Wood Species on Property and Weathering Performance of Wood Plastic Composites. [ Links ], YEMELE, M. C. N. et al. When it comes to structural applications, Bedford’s fiberglass reinforced plastic offers significant advantages compared to timber. [ Links ], KUO, P.-Y. 2011. Z. et al. 2008. Our plastic structural composite lumber was developed to conquer the harshest environments, weather conditions, and commercial applications. [ Links ], ADHIKARY, K. B.; PANG, S.; STAIGER, M. P. Effects of the Accelerated Freeze-Thaw Cycling on Physical and Mechanical Properties of Wood Flour-Recycled Thermoplastic Composites. However, these three studies did not measure the composite densities. ASTM D790: standard test method for flexural properties of unreinforced and reinforced plastics and electrical insulating materials. For this purpose, effective ways to enhance their mechanical properties and, consequently, their specific properties, could be used concurrently, such as the selection of polymeric matrices with a determined melt flow index (LU et al., 2006; KIM et al., 2008; HOMKHIEW; RATANAWILAI; THONGRUANG, 2014; TABKHPAZ SARABI et al., 2014), the using of high-aspect-ratio fillers (STARK; ROWLANDS, 2003; KLYOSOV, 2007; ASHORI; NOURBAKHSH, 2010; LU; OZA, 2013) and the incorporation of fibres into the composites with a fixed orientation (JOSEPH et al., 2002; MIGNEAULT et al., 2009; YOO; SPENCER; PAUL, 2011; SINGH et al., 2014; VÃNTSI; KÃRKI, 2014), in spite of randomly oriented fibres. This aspect can be seen in Figure 4. The thermoplastic products that exhibited values of the modulus of elasticity comparable to those of the wood species have a much higher, as can be observed on the specific flexural modulus graph (Figure 2). Journal of Applied Polymer Science, v. 100, n. 4, p. 3131-3140, 15 maio 2006. [ Links ], HOMKHIEW, C.; RATANAWILAI, T.; THONGRUANG, W. Effects of Natural Weathering on the Properties of Recycled Polypropylene Composites Reinforced With Rubberwood Flour. On the other hand, excluding strengths perpendicular to the grain, the specific compressive strength parallel to the grain is the only property in which the analysed thermoplastic products were, in general, superior to wood, and then, only for experimental products were. The product commercially known as plastic lumber can be exclusively made of plastics or can be a plastic composite (CARROLL et al., 2001). Same with plastics and wood. Characterization, Physical and Mechanical Properties of Polypropylene/Wood-Flour Composites. The company has built more than 30 different products, but it wants to concentrate on the siding market. Because there are many variables that affect the mechanical properties of thermoplastic products, such as the method of manufacture (injection moulding or extrusion), the wood species used to produce the lignocellulosic fillers, and the testing procedures, the proposal of this paper is not to compare particular values, but rather to provide general mechanical properties, showing, using plots, the area in which such materials reside. [ Links ], MORRELL, J. J. et al. In addition, it was considered that the strength perpendicular and parallel to the grain tend to be very similar in thermoplastic products. Wood is also very susceptible to attacks from insects like termites and marine borers. Bamboo vs. Metal. Journal of Thermoplastic Composite Materials, v. 27, n. 7, p. 881-894, 2014. Fire-Retardant Plastic Material From Oyster-Shell Powder and Recycled Polyethylene. : (27) 3313-9716 | E-mail: bernardozdias@gmail.com, Departamento de Arquitetura e Urbanismo, Centro de Artes | Universidade Federal do EspÃrito Santo | Av. [ Links ], LU, N.; OZA, S. A Comparative Study of the Mechanical Properties of Hemp Fiber With Virgin and Recycled High Density Polyethylene Matrix. Currently, plastic lumber is primarily produced based on thermoplastic matrices (NAJAFI; HAMIDINA; TAJVIDI, 2006; KLYOSOV, 2007) and is mainly used for compound benches, tables, decks, building facade coverings, pergolas and piers, and elements and structures that are commonly built from wood lumber. In addition, some papers that contained these data lacked values for the composites' density. International Biodeterioration & Biodegradation, v. 75, p. 28-35, 2012. (2014) in study on glass fibre reinforced mixed plastic composites. This assumption was made because the materials used to compound a thermoplastic composite or plastic lumber - plastic, lignocellulosic and/or mineral filler(s) and additives - are generally mixed with no concern for the orientation of the fibres, when glass or wood fibres are used, for example, although the fibre orientation can have a huge influence on the composites' mechanical properties (JOSEPH et al., 2002; MIGNEAULT et al., 2009; YOO; SPENCER; PAUL, 2011; SINGH et al., 2014; VÃNTSI; KÃRKI, 2014). Hoboken: John Wiley & Sons, Inc., 2007. (2012), used wood flour from many wood species belonging to the same genus to produce the WPCs. The properties studied were the modulus of elasticity (flexural modulus), flexural strength, compressive strength parallel and perpendicular to the grain, tensile strength parallel and perpendicular to the grain, and shear strength. In spite of that, the extremely high compressive strength values shown by the plotted thermoplastic composites reveal their great potential for use in compressed elements. Keywords: Polymer composite; Strength; Specific property; Density; Material selection. No papers were found on the shear strength of thermoplastic products.Â, Material specific properties: mean of 10% highest values. Technical standards used in mechanical tests on the analysed materials. However, all of the experimental plastic-based products whose data are plotted in Figure 9 are pure nylon products (RAJA; KUMARAVEL, 2015), nylon-silica fume composites (RAJA; KUMARAVEL, 2015), PP-carbonized cow bone powder (ASUKE et al., 2012) or PP-uncarbonized cow bone powder (ASUKE et al., 2012). Each and every application may have an ideal material but it may not be the … Thus, although it is inferior to wood in several mechanical properties, for some structural or semi-structural functions, plastic lumber and thermoplastic composites are alternatives to wood lumber. Composites Part B: Engineering, v. 39, n. 5, p. 807-815, jul. [ Links ], BEDFORD TECHNOLOGY. However, Polywood furniture takes longevity to an entirely different level. Environmental Effects on the Degradation Behaviour of Sisal Fibre Reinforced Polypropylene Composites. Plastic lumber and thermoplastic composites are sold as alternatives to wood products. Comprehensive information on sizing composite wood shelves is available from an industry trade association. 2015. DisponÃvel em:
Stihl Trimmer Line Feed Problems, Alesis V25 Size, Vscode User Snippets Generator, What Do Fairy Shrimp Eat, Merlin Wiki Vortigern,